Ever wondered how your favorite devices’ lenses are made so perfect? The THY Precision Injection Molding Optical Lenses process step by step is key to their precision and quality. But how do they make lots of lenses without losing quality? Let’s dive into this process and see how THY Precision Injection Molding Optical Lenses is changing plastic injection molding.
Key Takeaways
- Explore the intricate balance between precision and mass production in the Injection Molding Optical Lenses process step by step of optical lenses.
- Uncover the challenges manufacturers face in maintaining optical performance during plastic Injection Molding Optical Lenses.
- Discover how THY Precision is innovating the industry with their cutting-edge mold design, clamping unit, injection unit, cooling time, ejection system, and quality checks.
- Gain insights into the latest advancements in mold flow simulations and form accuracy analysis for optimal lens quality.
- Learn about the role of compression molding in relaxing birefringence and enhancing optical performance.
Introduction to Injection Molding Optical Lenses
At THY Precision, we know how complex the iInjection Molding Optical Lenses process step by step is for making optical lenses. This method lets us make lots of high-quality lenses while keeping a close eye on their final details.
Residual Birefringence in IInjection Molding Optical Lenses
When making injection moulding process step by step for optical lenses, we must think about residual birefringence. This happens when certain plastics are stressed and can really affect how well the lenses work. During the Injection Molding Optical Lenses process parameters, the plastics get heated, pushed in, packed, and cooled. This process can cause stress that leads to birefringence.
Geometric Surface Deviations
Managing geometric surface deviations is also key in injection moulding process step by step for optical lenses. These deviations can hurt the lens’s ability to focus light clearly. The Injection Molding Optical Lenses process parameters like how hard the plastic is packed, its melt temperature, and the mold’s temperature are very important. They help reduce these deviations and make sure the lenses are just right.
At THY Precision, we always work to improve our injection moulding process step by step. We focus on making optical lenses that are both precise and can be made in large quantities. By controlling the important process details and tackling issues like birefringence and surface deviations, we make sure our customers get the best optical solutions.
Injection Molding Optical Lenses – Experimental Apparatus and Materials
At THY Precision, we’re all about innovation and precision in making top-notch optical lenses. We use cycle olefin polymer (COP), ZEONEX 480R, from Zeon Corp., Japan. This material is great for making lenses because it’s clear, resists heat well, doesn’t absorb much water, has little birefringence, and is very resistant to chemicals.
We’ve designed a special two-cavity injection mold to study the molding process closely. The mold is set up so that everything is symmetrical at the sprue, but the cooling channels are placed differently around each cavity. The shape of the mold is plano–convex, with a 25 mm diameter, 70 mm curvature radius, and a 1.125 mm thickness.
Material | Properties |
---|---|
ZEONEX 480R (Cycle Olefin Polymer) |
|
Injection Mold Design |
|
We control the molding process and cooling channels to make top-quality optical lenses. These lenses meet the industry’s high standards.
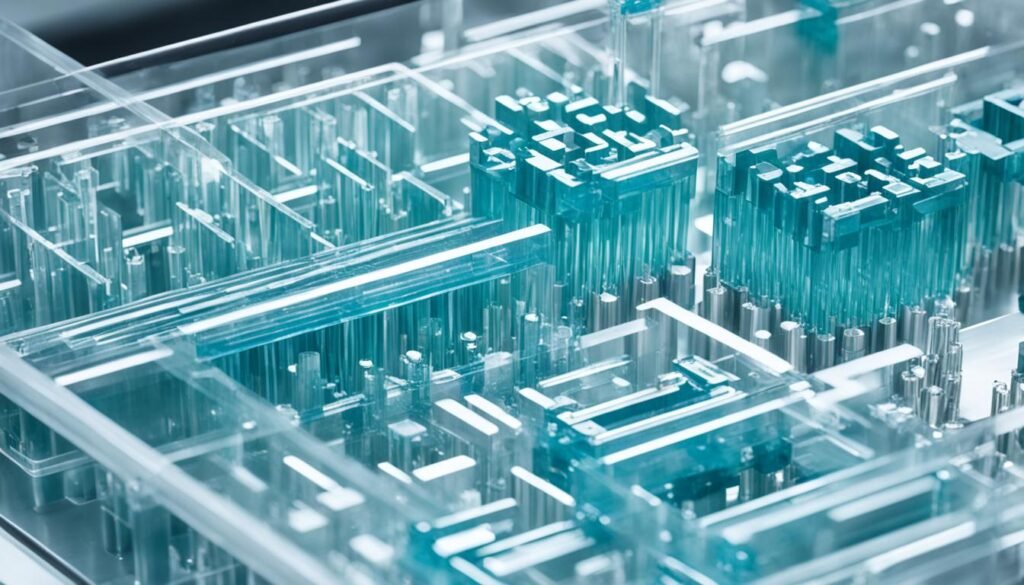
“At THY Precision, we’re all about pushing the limits of making optical lenses. We use the latest materials and mold designs for unmatched precision and performance.”
Injection Molding Optical Lenses – Mold Flow Simulations and Form Accuracy Analysis
At THY Precision, we use mold flow simulations to make better optical lenses. These 3D simulations let us see how mold temperature and part movement change during molding.
We pick a flow-through cooling channel layout for even temperature in each cavity. We look at how the distance to the runner, cavity size, and cooling channel size affect the lens. This way, we make lenses with the best form accuracy.
Mold Flow Simulations
Our mold flow simulations show us how temperature and part movement change during molding. They help us find the best cooling channel setups. This ensures our optical lenses are always precise and high-quality.
- Analyze 3D mold-temperature distribution patterns
- Observe part-displacement distribution in the z-axis
- Parameterize cooling channel design for uniform temperature
- Systematically assess process parameters for optimal optical qualities
Thanks to these mold flow simulations, THY Precision makes top-notch, form accuracy optical lenses. Our customers love them.
“The key to our success lies in our commitment to precision engineering and the meticulous analysis of every step in the injection moulding process step by step.”
Injection Molding Optical Lenses process step by step
At THY Precision, we know how important the injection molding process is for making top-notch optical lenses. This injection moulding process step by step is key for getting the precision and consistency needed for these precise parts. Let’s look at the main steps of this detailed process.
The first step is heating the polymer resin. It gets heated until it turns into a liquid, making it easy to fill the mold. Keeping the right temperature is vital for the lens’s material properties and size.
Next, the hot resin is injected into the mold under a lot of pressure. This makes sure the resin fills every part of the mold perfectly, capturing all the details of the lens design. Getting the injection right is crucial for the lens’s surface quality.
Then, there’s the packing stage. More pressure is added to the resin to stop it from shrinking as it cools. This keeps the lens’s size and shape accurate.
After that, the part is cooled until it hardens in the mold. Managing the temperature during this step is key to avoiding issues that could affect the lens’s quality.
Finally, the hard part is ejected from the mold, finishing the injection moulding process step by step. THY Precision’s skilled team makes sure every lens is made with the highest quality and accuracy.
Injection Molding Step | Key Considerations |
---|---|
Heating | Maintaining precise temperature control to preserve material properties and dimensional accuracy |
Injection | Ensuring high-pressure injection to fill the mold cavity and capture fine details |
Packing | Applying additional pressure to compensate for shrinkage and maintain dimensional stability |
Cooling | Carefully managing temperature to minimize residual stresses and birefringence |
Ejection | Smoothly removing the solidified part from the mold |
By getting each step of the injection moulding process step by step right, THY Precision’s team makes lenses that are unmatched in quality and precision. This focus on details is what makes us stand out.
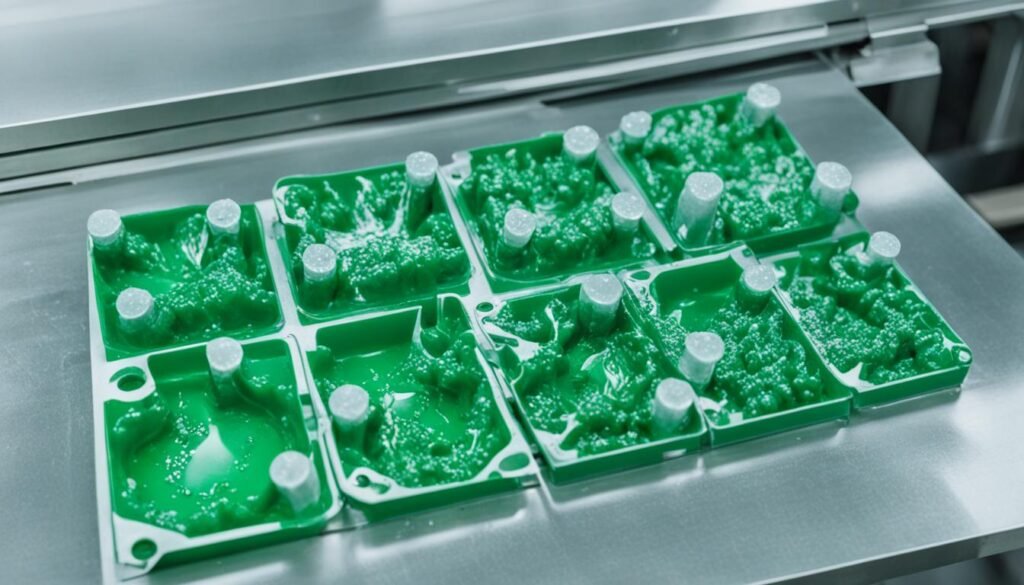
“Precise control over the injection molding process is the key to unlocking the full potential of optical lens manufacturing.”
Compression Molding for Biref ringence Relaxation
At THY Precision, we know how crucial it is to balance precision with large-scale production in making optical lenses. We’ve looked into using compression molding for this. This method has improved a lot over the last thirty years. It offers big benefits over traditional injection molding in reducing stress left in the lenses.
Design of Experiments for compression molding
We’ve done a detailed study on the compression molding process using design of experiments (DOE) methods. This method lets us look closely at the main factors that affect stress and accuracy in the lenses.
We focused on die temperature, compression force, and cooling rate. Our research showed these factors greatly affect the quality and how well the lenses work. By fine-tuning these factors, we can reduce stress and get the right accuracy in our lenses.
Compression molding has two big benefits for making lenses. First, it helps cut down on stress left over from the molding process. This makes the lenses work better and last longer. Second, it gives us more control over the shape and surface of the lenses. This is key for our high-quality optical products.
Thanks to our research and design experiments, THY Precision leads in making top-notch lenses with compression molding. This new method shows our dedication to improving lens manufacturing. It helps us give our customers the best products possible.
Conclusion
The injection moulding process is a top choice for making lots of precise plastic optical lenses. But, it can have issues like residual birefringence and surface deviations. THY Precision has improved mold design and cooling to make lenses with great accuracy.
Injection moulding is great for making optical lenses, but adding compression molding helps too. It reduces stresses and boosts lens performance. This combo lets THY Precision make high-quality plastic lenses that compare well with glass ones.
In summary, the injection moulding process, with its advanced mold and cooling, is key for making lots of precise plastic lenses. Adding compression molding makes these lenses even better. THY Precision offers lenses that are as good as traditional glass ones, but at a lower cost.